Predictive Maintenance for Cost Cutting with IoT
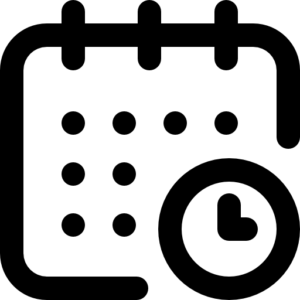

In any industry, there is a mechanism to prevent calamity from happening. This is where everyone focuses on the maintenance part. Maintenance what generally you do is reactive like fixing something when it goes wrong. Now, doing this kind of maintenance, as you can imagine, will cost a fortune. Not only does it affect your pocket but it also increases turnaround time as well. This delays the manufacturing process.
Utilize proactiveness, why not?
Since industries have been running for more than centuries, you can use historical data. The data can be used to anticipate when a part is likely to fail so that it can be replaced beforehand. This type of maintenance is called preventive maintenance. Here you can differentiate between expensive parts and cheap parts so that, based on their lives, you can try to replace them. But this is not a foolproof method as there might be times when parts can fail before scheduled maintenance.
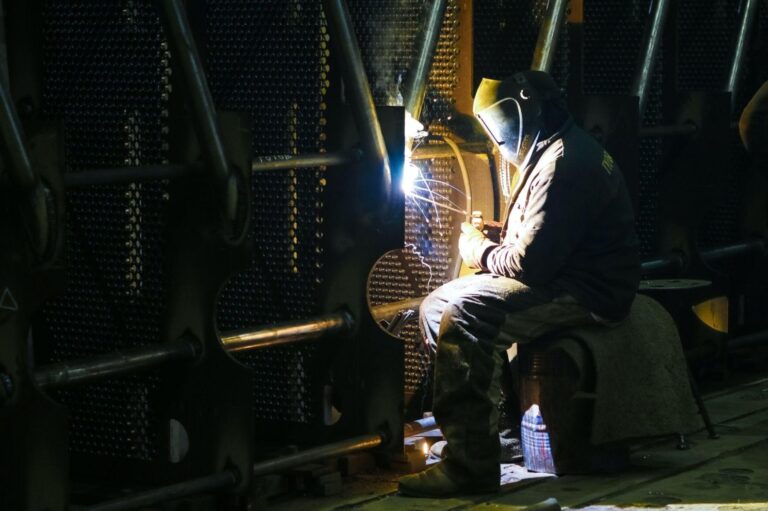
Failure of Preventive Maintenance:
● Over-Maintenance: In some cases, preventive maintenance can cause more harm than good. If equipment is serviced too frequently, it can lead to unnecessary downtime and increased costs.
● Incorrect Timing: Preventive maintenance schedules are often based on assumptions about the lifespan of equipment or the frequency of usage. If these assumptions are incorrect, preventive maintenance may be scheduled too early or too late, leading to equipment failure.
● Incomplete Inspections: If inspections are not thorough enough, potential issues may be missed, leading to equipment failure.
● Neglected Maintenance: Preventive maintenance is only effective if it is consistently applied. If maintenance is neglected or skipped, equipment is more likely to fail unexpectedly.
● Improper Maintenance Techniques: If maintenance is not performed correctly, it can cause equipment to fail sooner than if it had been left alone.
A smarter way to overcome these issues is to know the health of components in real-time. Imagine being able to know critical component performance beforehand, which can save you time and money. You can get early warnings to replace and monitor each part. This intriguing new level of maintenance planning is an important part of bringing smarts into smart buildings.
Potential to revolutionize
The Internet of Things (IoT) has the potential to revolutionize a wide range of industries, from healthcare to manufacturing. According to a recent study by McKinsey, one particular area where IoT can bring significant benefits is predictive maintenance. By using sensors and real-time data analysis, companies can reduce maintenance costs by up to 25% and increase production line availability by 5 to 15%. That’s a potential economic impact of $3.9 trillion to $11.1 trillion a year by 2025! This means that IoT-enabled predictive maintenance could not only save companies money but also contribute to the global economy by as much as 11%.
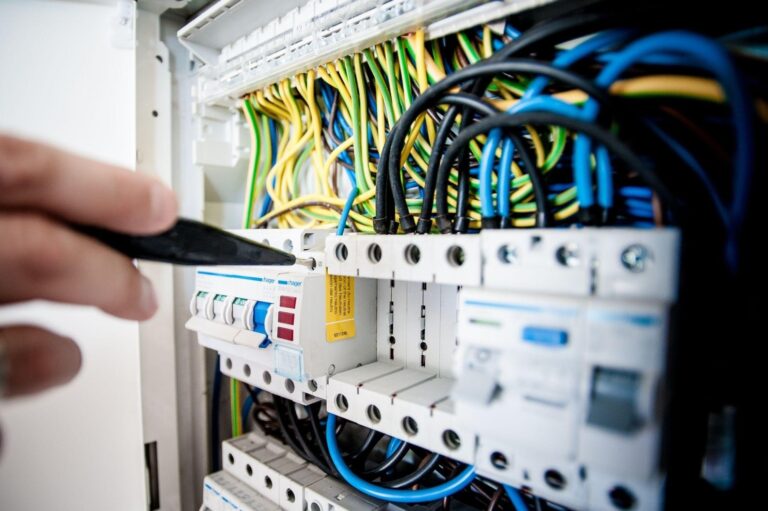
Benefits of predictive maintenance over traditional maintenance methods
● Focus on Prevention: Preventive maintenance is focused on preventing equipment failures through regularly scheduled inspections and repairs, while predictive maintenance aims to predict and prevent equipment failures before they happen.
● Cost-Effectiveness: Predictive maintenance can be more cost-effective than preventive maintenance because it avoids unnecessary maintenance and only addresses issues when they arise. Preventive maintenance, on the other hand, may result in unnecessary repairs and maintenance that can increase costs.
● Equipment Downtime: Predictive maintenance can help minimize equipment downtime by allowing maintenance to be performed proactively, while preventive maintenance may require equipment to be taken offline for scheduled inspections and repairs.
● Precision: Predictive maintenance provides more precise information about the condition of equipment, allowing for more targeted repairs and replacements. Preventive maintenance, on the other hand, may result in unnecessary replacements or repairs.
● Technological Advancements: Predictive maintenance relies on advanced technologies such as IoT sensors and machine learning algorithms to provide real-time data and insights into equipment performance. Preventive maintenance, on the other hand, typically relies on scheduled inspections and historical data to determine when maintenance is needed.
The potential benefits of predictive maintenance with IoT are not limited to just one study. A report by PwC found that implementing predictive maintenance in factories could lead to a significant reduction in costs by 12% while improving uptime by 9%. But that’s not all; the same report suggests that predictive maintenance could also reduce safety, health, environment, and quality risks by 14%. And if that wasn’t impressive enough, predictive maintenance could even extend the lifetime of an aging asset by up to 20%. With such significant benefits, it’s no wonder why more and more companies are turning to IoT-enabled predictive maintenance to optimize their operations and maximize their bottom line
Predictive maintenance involves using data to predict when equipment will fail, allowing maintenance to be scheduled before it becomes necessary. There are different types of predictive maintenance, including condition-based maintenance, time-based maintenance, and usage-based maintenance.
IoT technology allows you to collect data from equipment in real time, making it easier for you to identify potential issues. IoT-enabled predictive maintenance solutions can use machine learning algorithms to analyze data and make predictions about the health of equipment. Examples of IoT-powered predictive maintenance applications you see in the real world. This can include monitoring the performance of wind turbines, predicting equipment failures in manufacturing plants, and monitoring the health of vehicles.
Real-world Examples of Predictive Maintenance with IoT for Cost Cutting
A. A wind turbine manufacturer used predictive maintenance to reduce maintenance costs by 30% and increase turbine uptime by 20%.
B. A manufacturing plant used predictive maintenance to reduce maintenance costs by 25% and increase equipment lifespan by 20%.
C. To implement predictive maintenance, companies should start by identifying the equipment to be monitored, selecting the appropriate sensors and data collection methods, and choosing the right predictive maintenance software.
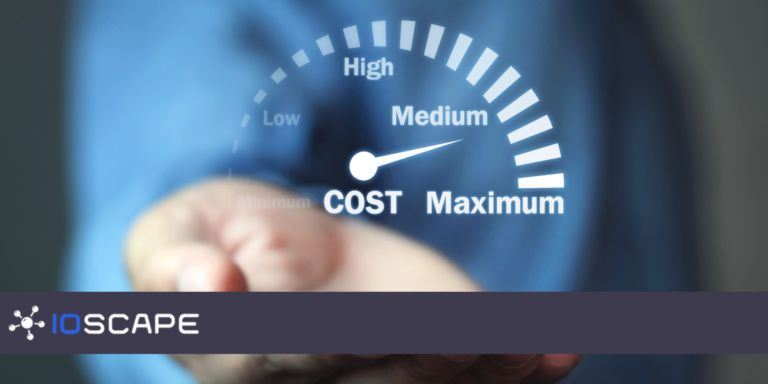
Predictive maintenance with the IoT is a powerful tool for cost-cutting and improving equipment performance. Companies that adopt predictive maintenance with IoT can reduce maintenance costs, extend equipment lifespans, and avoid unexpected downtime.
Are you tired of unexpected equipment breakdowns and unplanned maintenance costs? Do you want to optimize your production line and improve your equipment’s lifespan? Look no further than IOSCAPE.
At IOSCAPE, we specialize in predictive maintenance solutions for Industry 4.0. Our cutting-edge technology utilizes IoT sensors and machine learning algorithms to predict equipment failures before they happen. This means less downtime, increased productivity, and significant cost savings for your business.
Imagine being able to extend the lifespan of your aging assets by up to 20%, reduce maintenance costs by 18-25%, and improve uptime by 9%. These are the kinds of results that predictive maintenance can bring to your business.
Don’t let unexpected breakdowns and maintenance costs hurt your bottom line. Contact IOSCAPE today to learn more about how our predictive maintenance solutions can benefit your business. Let’s work together to optimize your production line, increase productivity, and save you money.